Last Post |
 wbain
|
11/18/2013 4:41 PM
|
I know this is old but my long body pump is missing it's little key in the pump section. I probably lost it when I took it apart a few years ago. I'm in the process of getting my Fintail operating so I need to check everything.
The pump section had lots of crud in it and gelled gas. I'm going to take the pump down to a well stocked hardware store to look for a candidate. I also checked the filter. It also had lots of junk in it and gelled gas. I cleaned that up.
I just bought a rust bucket 1960 220SE. It had a short body pump in the trunk, not connected, and on closer inspection, there is what looks like tar in it. I'm using acetone to soften the tar. I also bought some lacquer thinner. I'm going to try and take that one apart for cleaning.
Warren Bain '65 220S, '99 Volvo V70, 2002 Ford Crown Vic Police Interceptor
|
|
|
 Art Love
|
7/20/2008 4:25 AM
|
I got another one back together today. It wasn't leaking, but required new brushes on the electric motor. I took the oportunity to replace the bearings while it was apart. Anyone want to take bets that it will now leak[:D]? 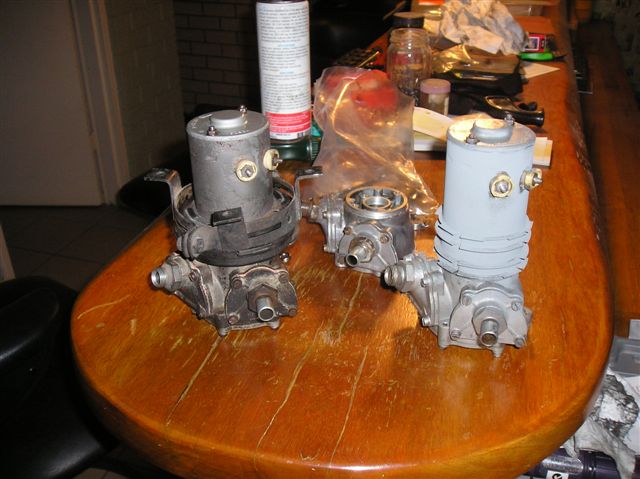 Art
|
|
|
 Art Love
|
7/19/2008 4:18 AM
|
Justin got the new bearings on the armature shafts, so today I finally got some time to get one of the pumps back together. There are a couple more to go. Hopefully one will not leak and it will go on #765. I'll get the next one done tomorrow. 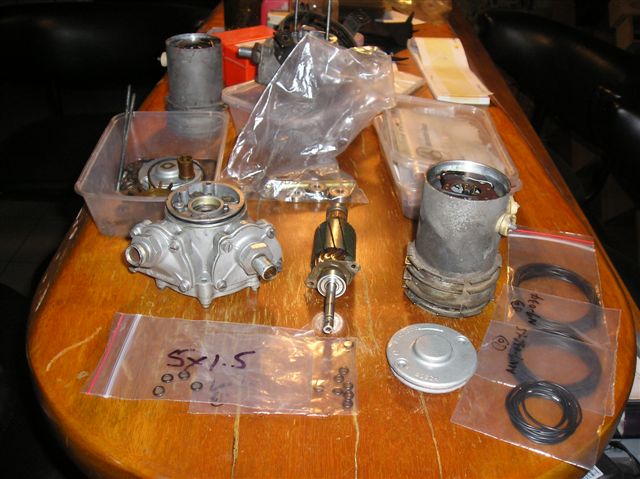 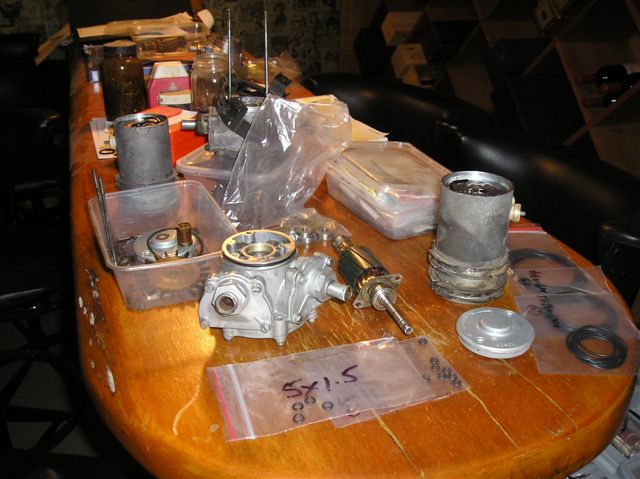 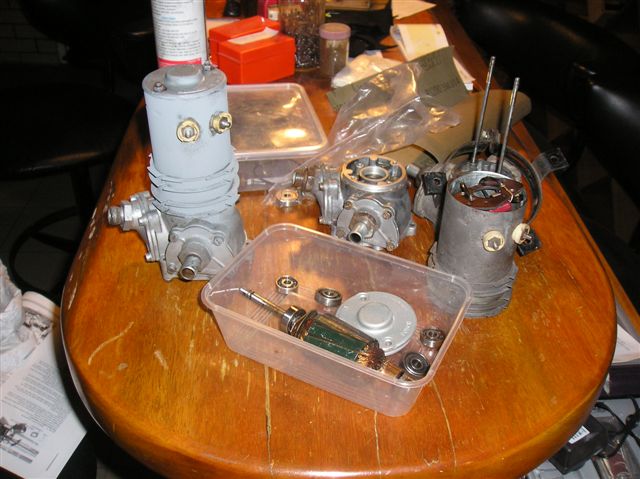 If any of you are wondering what that odd matt finish is on the electric motor housing, it is straight zinc to try to prevent further corrosion deterioration of the metal. I'll give it a spray of metal guard silver before it gets used. I don't have the metal guard can here at home; it's down at Three Point with the car. Art
|
|
|
 Art Love
|
3/20/2008 12:12 AM
|
Here's another part of the pump. This armature had severely worn copper brush contacts. There was a 1mm deep depression in the contact face. Unfortunately, I didn't take a picture of it. This picture shows the rebuilt contact points looking like brand new. The rebuild was done by Wacol Truck Electrics here in Brisbane. We'll replace the bearings and it is ready to go back into the pump 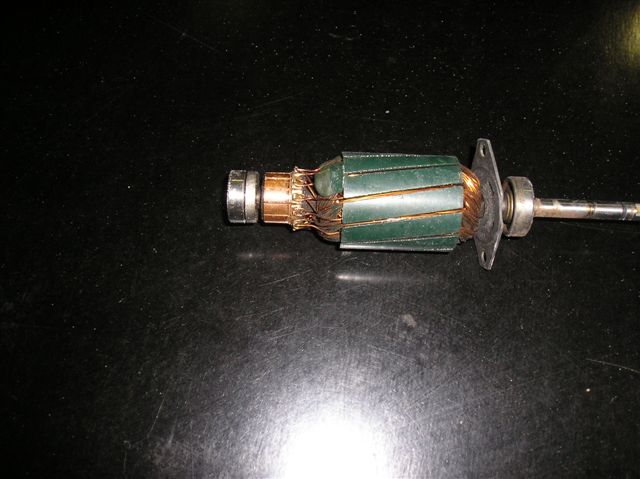 Art
|
|
|
 George Des
|
2/16/2008 1:43 PM
|
Art,
I'll have to look to see what size I've been using. The key thing is that the o-ring needs to be tight enough that it does not "spin" when you are sanding it down to size. What I do is chuck the armature in a drill press with the comm side of the armature nearest the chuck. What I will do is sand a little on low speed and then stop to check if the bottom portion of the bellows will just slip by the o-ring. It usually takes several stops and starts to get it just right. This sizing is critical and I was skeptical when the Tech Manual article was put together and did not include this becasue I've never been able to find an o-ring that will do the job right out of the "box"--maybe others have, but I've found the procedure I use provides great results and after you've done it a few times, it is no big deal to do. If the shaft o-ring is not tight against the bellows top edge, you will get leakage--maybe not right away, but sooner or later it will--best to do it right the first time. Hope this helps.
George Des
|
|
|
 Art Love
|
2/13/2008 8:18 AM
|
I'm doing another follow up on this. George Des mentioned sanding down an O ring for the shaft seal at the bottom end of the bellows seal but did not say what he started with. In the article I mentioned that I had published in Lode Star #43, a condensed version of the advice on the Pagoda Roof Club website, there are typos. The same error appears on the Pagoda Roof website. In the early discussion it it says that the O ring can be replaced witha 5x1mm. I believe this to be wrong. This size O ring is too small in the groove on the shaft, even if its outside diameter may be about right. In the assembly section, it says to use a 5x1.5 O ring. There is another typo in the Lode star article, calling it a 1x1.5. There is no way that the bellows seal will go over a 5x1.5 O ring. This size O ring certainly fills the cutout in the shaft quite well, but is far too thick to allow the bellows seal to pass over it. It has to be sanded down to about one third to one half of its original thickness to do this. I did this by mounting the O ring on a Dremmel and applying 80 and then 120 grade sandpaper to the spinning O ring. In my earlier attempts, I trial fitted the O ring repeatedly to the shaft, but when I got a bit smarter, I trial fitted it to the bellows seal off the shaft. Art
|
|
|
 Ron B
|
1/28/2008 6:31 PM
|
Isn't the seive just pushed into place and held there with little lugs on the seive body?
...There are old cars,and then there are Classics..(Mercedes Benz Ad. 1999)
|
|
|
 Art Love
|
1/27/2008 11:36 PM
|
Fuel pumps one day, dentures the next[:D][:D]. I've got two pumps in bits at the moment. It's interesting what you find and what you learn. I got one in bits that someone had butchered apart. Rather than patiently soak, spray with penetrating "oil", tap and prize apart, the bottom bolts were angle ground off, the inflow pipe hex had been attacked with a chisel etc. Fortunately, all the bits were still there and everything is rebuildable.
Took the two pumps over to Justin's shed this morning. The butchered pump had the top bearing stuck in the top lid of the pump. It had come off the shaft stuck in the lid instead of stuck on the armature shaft. Being a surgeon, I had NO idea how to get the bearing out of the lid. Justin packed the shaft hole with soap and started to pound on the soap with a drift and lo and behold, the bearing gradually came out. I learned something new[:D].
I bought a couple of new inflow pipes from Tom Hanson, part 000 997 59 72. Neither Justin nor I could see just how the brass sieve in the pictures above came out of or fitted into them. I was concerned about damaging the sieve, so we decided to reface the hex on the existing one where it was chiseled and reuse it. Does anyone know how these two components come apart and go together?
The electric motor housing from the one with the clogged sieve that I took apart was FULL of carbon dust. The armature and brushes were in good condition despite that. We've cleaned both motor housings out and Justin will take the two armatures and housings to an electrical shop. The second armature has wear a couple of mm deep where the brushes rub and will need to be rebuilt. All 4 bearings are shot and we will replace them. Then I'll put the whole lot back together again and we should have a couple of good pumps. Art
|
|
|
 Ron B
|
1/27/2008 8:38 PM
|
I just used ordinary detergent too with a little added turpentine. I have heard of others using alchohol based carb cleaners etc but there is a very real risk of explosions as the stuff becomes aerosol.
...There are old cars,and then there are Classics..(Mercedes Benz Ad. 1999)
|
|
|
 Chris Johnson
|
1/26/2008 4:07 PM
|
Ron, what were you using as a cleaner in the ultra-sonic unit?
I have a three-quart unit, and frequently use it with standard liquid detergent (no lemon scent though!), and diluted Oil Eater solution. Tank and fuel pump screens I generally clean with carb cleaner.
When I got the ultra-sonic unit, I bought four gallons of the recommended solution from the manufacturer, but UPS delivered it to a neighbor (for whatever reason) and it sat on his porch frozen solid for four months before he sobered up enough to realize it was there.
Chris Johnson If you aren't constantly impressed with your car, then it needs fixing. 100.012-12-000790 100.012-12-000867 109.018-12-000010 109.018-12-000019 109.018-12-003834 www.300SE.org
|
|
|
 Ron B
|
1/26/2008 3:20 PM
|
Art..do you know any dentists? ,ask if you can clean it in the ultrasonic.It's how i cleaned mine up. comes up like new but my machine is Kaput now after fluid leaked into the guts of the thing..[:(!][:D]
...There are old cars,and then there are Classics..(Mercedes Benz Ad. 1999)
|
|
|
 Art Love
|
1/26/2008 2:18 AM
|
Here's a follow up. 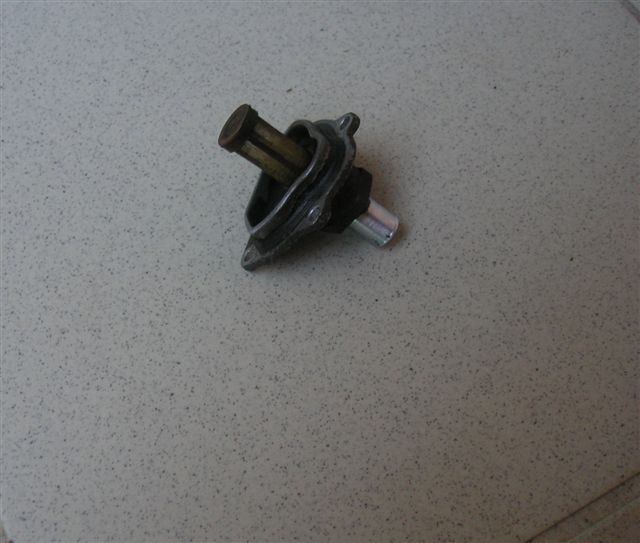
|
|
|
 Art Love
|
1/25/2008 3:41 AM
|
I recently posted on the thread in General Discussions on the Fuel Injected Roundie Restoration that Craig Tucker started about crud in a long body pump that I am working on. I was silly not to have taken a picture of the crud in the inflow pipe and filter at the time I found it. It filled the inflow pipe and brass sieve. After several days of soaking in ATF, brushing with kero and blowing out with the air compressor, I am part way through cleaning the impacted crud from the brass gauze filter. I thought it more appropriate to continue the thread here with a couple of pictures. One picture is taken from the top and the other from below. You can see that I have made a lot more progress on the upper side of the sieve than the lower, just an indication that the lower side was much worse. It is no wonder that this pump failed to deliver. Art 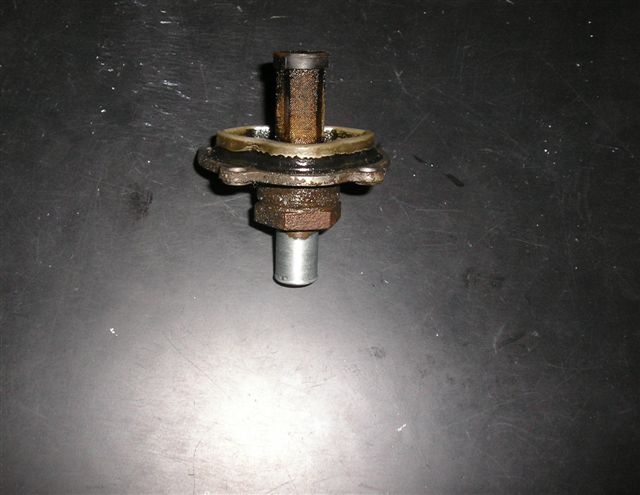
|
|
|
 Art Love
|
7/20/2007 3:50 AM
|
The article on rebuilding the long pump is in the Autumn 2006 Lode Star (Issue 43) on pages 11-12. I got it from the local M-B Club magazine. Art
|
|
|
 George Des
|
7/19/2007 9:57 AM
|
I saw the locating washer that MYPOOR 6.3 mae from the feeler guage and I can relate. I had many of these parts go bad as I previously noted and since it plays such a key role in the working of the bellows you just need to have one if the tab is broken. AS I alos pointed out, the tab gets broken when soemone tries to force a pump that has a stuck vane. I've also seen where these get broken when trying to remove the bellows from the shaft of the armature. If you aren't aware of the tab and try to twist the bellows off while pulling on it, it will result in a broken tab and useless locating washer. I had several dozens of these made should I run into the problem again anytime soon. Another often overlooked part is the small rubber o-ring on the shaft. This o-ring seals the top portion of the bellows to the shaft. When removing the bellows for whatever reason, the rubber o-ring never quite seals again the same way and should be replaced. Since it is difficult to find an exact size replacement of this seal, I have to use an o-ring with an undersized inner diameter and oversized outter diameter wet sanding it down with fine sand paper to eefect the proper fit between the shaft and the bellows seal--this is purely a trial and error process.
George Des
|
|
|
 bwostosh
|
7/19/2007 6:51 AM
|
How about a group parts inventory?
I'd finally get a complete garage inventory for posting. Another reason to get up in the morning. These cores are becoming worth it. They could be rebuilt, boxed and stored. I have major components needing clean, dissass., paint, check, replace, assemble
Those bellows stumped me too, tricky formed metal part
Brian O.
|
|
|
 abl567
|
7/19/2007 3:38 AM
|
The rebuild kit idea would go well in the Group store forum.
6.3 #2723, my first classic Benz
|
|
|
 james lawson
|
7/19/2007 1:43 AM
|
Chris, My Poor 6.3 recently did this and posted the process he went through and how he made a seal from a feeler gauge. I think there was also an article in the Lode Star recently.
jim
|
|
|
 George Des
|
7/19/2007 1:05 AM
|
Brian--the bellow themselves are not available as far as I know. The parts I referred to in my earlier post can be gotten from a number of different suppliers. I have a few sets of new brushes--can get more--can get the seals and bearings and have plenty of those locating washers--no in line filters or bellows though. Also, the armatures can be rebuilt if the comms are too far gone.
George Des
|
|
|
 bwostosh
|
7/18/2007 10:53 PM
|
Good to know, that there is someone else there. I fixed a few of those brass bellows 25 years back. I now have 6 of those long styles, needing work/rebuild. The originality guys need those. Had an offer for $400 for a non leaker. Had to save the only good one for myself. also have 7 newer styles needing work. How do we get a batch of parts?
Brian O.
|
|
|